
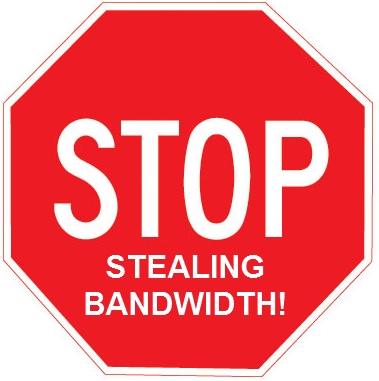
pcassidy111
Members-
Posts
61 -
Joined
-
Last visited
Content Type
Profiles
Articles
Forums
Gallery
Everything posted by pcassidy111
-
Leaving your wireless network open is no big deal as long as your computer'S firewall and virus definitions are up to date. Living in the 'Silicon Valley' everyone has wireless networks-8 unsecured ones (and only 1 secured site) available from my easy chair-and most of my neighbors are techies. Some cities here are even going to city wide open access wireless networks. So some kids are out 'WAR'ing on my IP address, they cannot access any of my computers and if the Fed's come knocking because of some illegal activity on my IP address they will find no evidence of it on my computers.
-
What I have done in the past for this code on 4.6L is to monitor the frequency of the signal with a graphing multimeter, looking for dropouts. The frequency should remain constant for a given rpm. If the sensor tests good I replace the pigtail to the sensor (plug and about 6 inches of wire-a common problem area on the town cars and crown vics.), did he do a wiggle test and look for drop outs?
-
Had a small bead blaster that used walnut shells to clean intake valve deposits. Safe because any media that was not removed with the vacuum was burned up in the engine.
-
Try Chrysler Top Cylinder cleaner spray or Delco X66A or X66P. Both of there products are made to put into running engines but they also work well when sprayed onto carbon and allowed to soak in and soften it. I use scrapers or a brass vegatable brush to help remove it. I use brake clean to wash away the loose carbon
-
Hot CAC Tube Won't Stay On
pcassidy111 replied to Keith Browning's topic in 6.0L Power Stroke® Diesel Engines
Through my limited experience on the 6.0L (I work at an independant) I have found it necessary to retorque the hot CAC tube hose clamps up to 6 times over a 2 day period before they will maintain 100-106 in/pounds, especially when using new clamps. I have found that after torquing the clamps to 106 in/lb and going through 1 engine warm up cycle the clamps 'relaxed' to 74 in/lb. I know it is probably not 'real world' to be able to retorque the clamps over a 2 day period for you. All of the trucks that I have done this on belong to the steel yard and tow yard down the street so I just tell the dispatchers that to have the drivers stop by on their way to their jobs. No oil leaks or tubes blowing off so far. -
What is the o2 sensor doing? Have you confirmed that bank 2 is actually rich? If you create a vacuum leak can you get the bank 2 o2 sensor to go low? Is the o2 sensor plug covered with oil, allowing voltage from the o2 heater to bleed over to the o2 signal wire? No moisture or other contamination in the loom plugs causing voltage to 'leak' over to the o2 sensor wire? Had a truck one time that had transmission work done and they switched the o2 sensor plugs-caused wierd problems. Had another truck that had a tranny done and they did not put the o2/transmission wiring back properly, melted on the exhaust and caused a low voltage (around 1 volt) to be applied to the o2 signal wire-indicating a rich mixture and causing a lean miss.
-
Jim, thanks for the info. I use MODE 6 quite often to diagnose intermittent MIL complaints (when interpretation information is avaiable since mode 6 data is not yet standardized). Do you know what the duration of failure time is to set an under or over boost code so I can get an idea of when to trigger the 'snap shot' (I don't have a 'flight recorder')? I like that 'not being confident' phrase, sounds better than 'unable to duplicate complaint'. HGM, I will try your preconditioning procedure prior to running the KA test though my problem is very intermittent. Trying to simulate the failure condition is the most dificult part of diagnosing intermittent no code driveability complaints. Numerous times I have driven customers cars back and forth to work (with their permission), scanner, o-scopes and volt meters on the the dash looking for intermittent problems-on my own time but the customer's gas. I solved my 'unpredictable damping' condition by adding a shock washer to each side of the frame mounted bushing.
-
not all trucks that come in with a turbo problem come in with a STUCK turbo and they test good in the service bay. I have had several that required extensive road testing and one I sent off on vacation with his 5th wheeler and our VCM My truck has only had this problem 2 times in 17K miles of towing, not likely it will show up on the shop floor. Both times towing over the Sierra Nevada, once each way. Next trip I will have the scanner hooked up and try to duplicate the condition on the same hills. Have you ever looked at MODE 6 data when diagnosing this type of problem and does anyone have the PID parameter information (min and max values) for the codes for under and overboost? How long does the condition have to last to set either a hard or pending code? I cannot find information as to whether these are 1 trip or 2 trip set codes. Never tried to access MODE 6 data on this vehicle, may not be able to do it with the scanners that I own but I do have access to Ford scanners (WDS and IDS)-do either of these scanners support MODE 6 data?
-
Any new information on this condition. 2 times on my own truck I have experienced the condition that paulh and Ford DR have described. Light accel, 1800-2000 rpm, 40-50mph, 9K# trailer at 7 to 9K feet altitude, only 10psi of boost, exhaust temp 1200+ degrees F. I thought that I caused the problem by trying to drive the truck like it had a gas engine. The second time (8000feet, 7% grade, hot engine, 80degrees ambient temp, light accel) that it happened I pulled over, did not shut the truck off, then restarted the climb to the summit with no problems. No codes and I have not reflashed the pcm since new (6/05). The first thing that I will do is have the latest flashes done for my T/H issues then recheck but has anyone else tried to diagnose this problem or has a reflash been issued specifically for this complaint?
-
Keith, my truck is a 2005, in possession for 13 months and has 15K miles on the odo, would this get a new engine or a short block? My preference is to keep the motor that I have now if it can be sucessfully repaired.
-
After repairing all of the oil leaks that I could find and being dry for 2000 miles, my personal truck now has a bed plate seal leak behind the starter. After cleaning the area and running the truck on high idle, nose up for 20 minutes I can see oil leaking out around the bed plate bolt behind the starter. CKP and CMP dry and no leaks above it (glow plug harness, CAC etc). There is oil on the rubber bellhousing plug but I don't think it is the RM seal, HPOP cover etc because the oil would have to travel uphill on the bed plate seam to get where I can see it leaking. I added dye this morning to confirm my diagnosis. I will send this repair to Ford but I have a couple of questions. regarding the repair. Has anyone seen a bed plate seal leak on a block with no machining defects? If it requires a short block is it new or reconditioned? (MY 2005, 15K miles) If it is a reconditioned SB is there any way to persuade them to install a new short block? I'd like to get 150K miles out of this truck and I feel that installing a reconditioned SB may not be in my best interest. As always thanks for the help and information, I still have another year or so to learn about these engines before my customer's trucks start coming out of warranty.
-
Oil filter housing broke
pcassidy111 replied to pcassidy111's topic in 6.0L Power Stroke® Diesel Engines
Those tabs depress a lock mechanism that allows the stand pipe spring to compress. If there are 2 large pieces of flashing between the tabs-like on the Motorcraft filter the tech tried to install the spring will not compress. His mistake is pushing to hard-have to get him off the steriods. Going to check into having Motorcraft cover the repair. Thanks for everyones input. -
Oil filter housing broke
pcassidy111 replied to pcassidy111's topic in 6.0L Power Stroke® Diesel Engines
gasgasman, there was nothing stuck in the tower. Do the 4 tabs on the inside of the filter (around the oil bypass hole) need to depress the 4 spring loaded pads surrounding the oil bypass valve before the large spring can be depressed? While checking the oil stand pipe on my vehicle I noticed that intermittently it would be difficult to depress with the filter and sometimes I would hear a snap before it compressed. Does the sliding mechanism inside the spring sometimes bind up? I know this post is 'much a do' about a simple service (LOF) but it is turning into an expensive repair that we do not want to repeat. -
Super Duty Cab Removal
pcassidy111 replied to Keith Browning's topic in 6.0L Power Stroke® Diesel Engines
Pictures would be good. Thanks -
Super Duty Cab Removal
pcassidy111 replied to Keith Browning's topic in 6.0L Power Stroke® Diesel Engines
Anyone pulling cabs to replace the gas motors? We don't have the special lifting adapter for the 5.4L and sometimes the engine comes out with a bang. Installing the motor is tricky also, eveything has to be lined up and go in straight-not just aslam dunk and wrestle it in like the overhead valve motors in the old style cabs. -
Lube tech was changing the filter on a 6.0 and he broke the plastic spring loaded assy (standpipe?) that goes up into the filter. Claimed that the spring was not compressing so he pushed a little harder then snap-now the spring won't stay in the housing. The shop owner asked me to pull the filter out of my truck and investigate the problem-yea, oil change on the owner's dime. It appears that the 4 tabs on the inside of the filter depress 4 flats on the spring loaded tower before it will 'unlock' and allow the spring to compress. Is this correct? Did the tech do something wrong or is there a problem with the filter assy or Motorcraft filter? I did notice on my filter that sometimes it was difficult to compress (but I did not push hard enough to break anything) then something would snap and the spring would then compress easily. Any information would be appreciated as we do not want to repeat this costly mishap.
-
This buzzing noise, is it pretty noticable on decel at freeway speeds when the fuel is shut off? I test drove one of our fleet account trucks (2005 F450) on the freeway and heard a buzzing noise, not the normal 'air pump' noise on decel. Don't have a bidirectional Ford scanner so I cannot test as directed in the TSB but I would like to inform them of a pending problem if one does exist. There are no starting problems with this truck, 1-2 seconds of cranking hot or cold. Thanks for the help.
-
never ending CAC tube leaks
pcassidy111 replied to pcassidy111's topic in 6.0L Power Stroke® Diesel Engines
Put a new turbo end hose on my personal truck, cleaned the mating surfaces and tightened all the clamps to 106in/lb. So far I have retorqued the camps to 106in/lb 7 times over a 4 day period. They seem to 'relax' to around 90 in/lb-maybe this is why they leak when only torqued to spec 1 time? I do not see the hoses being cut into and I don't think the clamp is failing (becoming bell shaped as some have said will happen when this clamp is overtorqued). I don't think that I am crushing the tubes because I am not exceeding the torque spec. Has anyone else experienced this 'phenomenum'? Good news is no leaks so far. -
never ending CAC tube leaks
pcassidy111 replied to pcassidy111's topic in 6.0L Power Stroke® Diesel Engines
My problem is at the turbo end of the hose (at the turbo), it is dripping and I want to fix this leak before looking any further. Jim, you use Hightack red, in the spray can? I am going to try a new turbo end hose on my truck and if that fixes my leak then I will use a new turbo end hose on the other truck. -
I have installed new clamps, torqued to spec (109 inch/lbs), warmed up engine and retorqued the clamps and I still have an oil leak from the CAC tube (hot air side) I have this problem on 2 trucks that I have cleaned/tightened the CAC tube clamps and they are both leaking at the turbo clamps. Any tricks you Ford Techs are using to prevent leaks? I am not a Ford dealer and am just starting to see these engines. Any suggstions would be appreciated-I hate comebacks. /forums/images/%%GRAEMLIN_URL%%/banghead.gif
-
Jim, somewhat off topic but what is a 'pay period' for you-1 week, 2 weeks? Is it 100 chargable hrs per man or are you a team? Are you a 24/7 shop or do you have keys?
-
TSB 05-13-5 clamp problem
pcassidy111 replied to pcassidy111's topic in 6.0L Power Stroke® Diesel Engines
problem solved, parts dept said there was a mistake in the exploded view they faxed me and the correct part is on the way. -
Changing the clamp on the hot side CAC tube at the intercooler (large clamp on the intercooler inlet) to cure a leak. Ford parts crossed the number on the old clamp and sent me a 6C3Z-6K786-CA as per the TSB. Problem is the clamp is too small, it is larger than the other clamp listed in the TSB but it does not fit around the silicone hose when it is installed on the intercooler-even if I back the nut off so it is engaging only 2 threads. If I remove the nut and spring and put the clamp on I cannot compress it enough to reinstall them-and the two ends of the band clamp are not even close to engaging each other. Are these clamps an extremely tight fit, do I need to install it without the spring first to stretch it or do I have a defective clamp? Looking at it even if I could get the nut started I don't think that the ends of the band will slide over each other before I reach the torque spec. Do I have a manufacturing defect? They can get me the same P/N clamp that I am replacing, but I am replacing it because the ends of the band touch when tightened so-I may end up with the same problem, hence the updated P/N clamp. Any help from you Ford techs who have installed these updated clamps would be greatly appreciated-I work for an independant shop and am just now starting to see these engines for anything but oil changes. Thanks for the help, Pete Thanks, Pete
-
Thanks for the info Jim, figured I'd practice this repair on a customers truck before I do it on my own. /forums/images/%%GRAEMLIN_URL%%/smile.gif I did not notice the word'turbo' on the boot. One side of the boot had staples holding the clamp on it-I will look under the clamp tomorrow when I replace it (the threaded portion is bent). I am also replacing the clamp at the CAC (hot side) because the clamp appears to be streched-the ends of the clamp make contact at 90 inch pounds-the boot and CAC inlet look ok. Met some people visiting from Slave Lake area last week-laughed when I told them we are currently experiencing a major cold spell with a low of 37 degrees F at night. I guess it gets pretty cold where you are at.
-
I am R&Ring the Hot side CAC tube to repair an oil leak on a 2005 PSD. The TSB states torque the HOT CAC clamps to 13 MN (115 inch pounds). Has anyone had the intercooler inlet crack when going this tight on the clamp at the intercooler? I am also tightening the cold side CAC clamps to 12Nm (as stated on the tube) but I cannot find a torque spec for the cold side CAC tube clamp at the intercooler outlet-is 12 Nm too tight? Can anyone give me the spec for the cold air CAC tube clamp at the intercooler? Also, is the white line on the silicone tube at the turbo (not the lines indicating clamp placement, the line perpendicular to those lines) supposed to be orientated straight up? On this truck it is not but the line on the tube at the intercooler is. Thanks, Pete