
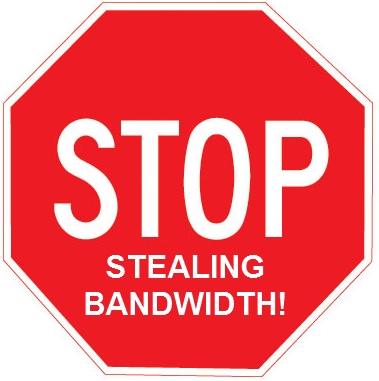
blown99
Members-
Posts
315 -
Joined
-
Last visited
Content Type
Profiles
Articles
Forums
Gallery
Everything posted by blown99
-
Wondering if anybody on this board is from the Binghamton, NY area? I have a good friend that lives in the area that has been having trouble with his 6.0. His current repair shop is not up to par. Any names of a good dealer in that area? I don't know the area so I could not help him much. Figured somebody from here may work out that way. Thanks
-
There was a very tiny amount of debris on the IPR valve screen. Not enough to block off oil flow or cause a screen to be sucked in. Looked more like the debris you find on the oil resivoir screen vs metal shavings indicating the failure of a hpop.
-
I've got an 03 vt 365 with a no start due to low icp while cranking. Makes 250-400 psi. I pressure test the system through the plug in the rear of the HPOP cover, energize the IPR valve and I have a big leak. Remove the intake and the pump cover. Remove the stc type joint and find the ring inside broken. R&R the pipe from the pump to the branch tube. At this point we have nothing to pressurize the system with the cover off, so I reinstall the cover, pressure test and I still have a leak (with the ipr energized) Boss says to reassemble because I found the broken part, guess what, still a no start. Tear it apart. This time a made a fitting to pressure test the branch tube on out the rails. Zereo leaks. (I did have the valve covers off before and inspected for leaks by cranking the engine with the IPR valve energized. No Leaks were found then) I then shot air into the port on the stc tube that feeds the ipr valve (cover still off) and had air blowing out the hpop seal. I though great, here is the leak, ordered a pump, should be here on Monday. Then I look on this board and see a posting from a few weeks ago about dead heading the 03 pumps and tsb's saying that leakage around the pump seal is normal. So how much is normal. This was a large enough leak to (with the hpop cover on) blow oil out of the turbo oil feed line. With the hpop cover off, it would shoot oil onto the firewall. This is the first 03 series engine I have seen with a high pressure oil system issue so my experience is a big fat 0. Ideas??
-
Do you guys normally find the heads to be warped when there is a head gasket failure? I was just talking to our CSE yesterday asking him why I never see any VT365's with head gasket failures like you ford techs see, and guess what came rolling in the door today! I've pulled many 365 heads in the past, but not for pressure in the cooling system. CSE also told me that the late 06 and 07 engines received head studs from international. Any of you guys see these in the fords yet?
-
Pulled the fuel filter out. Figured I would inspect the heater element etc for rust. I have seen these rott out in the international applications. Everything looked perfect. Even my filter looked brand new, and it was a year old. That fault would be generated by the dash logic?
-
Had one today that was similar. Engine would develop a miss at operating temp only under a load of 80% or greater. I got the engine up to operating temp, removed the valve covers, removed the ecm relay so the engine will not start, full field the IPR valve and jumped the starter to crank the engine. Found two injectors to be leaking excessivly. Techline wanted a complete set so that is what it got. All is good now. No 333 code on this one though, but icp was erratic only when it was skipping.
-
I didn't get any faults. Educate me on the p0460 code (don't have a book in front of me). This was my own truck. With fuel prices being high, the tank has been kept low and I used it only a few times this summer. I'm thinking condesation/humidity did it in. I use lots of additive every time I fuel up. We do have a lot of 466's blowing tips off lately, so I know what you mean about the poor fuel.
-
Thank you for the specs. Since my last post the sender has not gone to empty, it has been staying around half or full, when the tank has about a 1/4-3/8 fuel. I drove the vehicle around until the problem occured, unplugged the sender and checked the resistance at the sender. Found the sender resistance to be very high, 5k ohms. Resistance would slowly and steadily climb with the meter on it. Dropped the tank and removed the sender. Found rust on all the sender components. Disassembled the sender and gained access to the wiper assembly. Found poor continuity on the ground side. Cleaned all parts, assembled and tested. Installed into the tank and rechecked the sender readings, still ok. Tommorrow I'll reinstall the tank and road test.
-
Unfortunatly I don't have accesst oany of the high tech ford gadgets. I am leaning towards a sender even though I have not done any diag yet. Yesterday it read full for a while then dropped to empty. Key off for a while, go back to it and it read the correct reading for the rest of the time in use. Are there any computers that control this reading? I thought the dash was flashable??
-
02 f-350 diesel single fuel tank. Fuel gauge reads normal, then drops to below the empty mark (low fuel light comes on). Let the truck sit for about an hour come out and all is normal, drive it again and it acts up again. I am thinking about throwing a resistor across the sender connector terminals and going for a ride to try and rule out a harness issue. Anybody seen this before?
-
VT-365 Cylinder Contribution
blown99 replied to Keith Browning's topic in 6.0L Power Stroke® Diesel Engines
If both values are below the deviation then the injector is bad. I am not sure how the ford system works, but with MD, you calculate an average of the eight injectors, and take the worst (below the deviation value) as the bad. You can install the replacements and perform the disable test again, and fail several more. It used to be, if I saw an injector that was at, or just a hair better than the deviation value, I would change it. International changed their policy back in November. If you have one bad inj. replace it. Any more than one bad, then all eight get replaced. International still has problems with rust in the fuel tanks. I've had several 466 egr motors that were hard starting due to rust built up around the injector inlet screen. -
I see this on a regular basis in the international chassis. There is a link underneath the injector solenoid that wears. When the solenoid is engergized it is supposed to pull up on the link and allow injection to take place. When the link is worn the clearance is greater allowing more cold heavy oil to be between the link and the solenoid. The solenoid can not pull up the link to allow for injection. If there are no codes stored, and I can't hear the buzz during the buzz test, then I disconnect the glow plug system and get the engine to run on starting fluid. This will always trip the CEL with a 525 code, idm current high. International offers a tool kit that they will send to you that requires you to remove the solenoid and reshim the solenoid to the link. It can be done with the injector in the engine.
-
I've had two in a row now that had the heads of the bolts shear off the stc/branch tube when the fitting broke and the bracket slammed into the flywheel housing. They are cast iron on the IH, bit stronger than the aluminum that you guys see.
-
I had the pleasure of installing one of these new kits today. I thought it was a bit more difficult vs the snap together + bracket design. It requires you to measure the depth of the STC joint with a gauge bar, install the pump, install one stc joint ot branch tube bolt, then install a tool (anti rotational tool) that threads into the other branch tube to joint hole. Then use the flare nut socket to torque it. The flare nut socket does not fit due to the casting of the block on one side. This required me to grind the socket to fit. The torque spec is 53 ft/lbs. The anti rotational tool bent. A couple more times and I am sure it will break. A one foot bar attatched to a 4mm ? bolt that is threaded into the branch tube. Of course the bolt section is going to bend at 53 ft/lbs. The instructions also tell you to bend the branch tube to make it fit.
-
This cant be just our shop seeing this
blown99 replied to Tony302600's topic in 6.0L Power Stroke® Diesel Engines
I take it, you have to disconnect the electric fuel pump to prevent fuel from being pumped up to the filter housing? The international chassis uses a gear driven fuel pump; probably have to come up with some way to shut off fuel going to the filter housing. Thanks. -
This cant be just our shop seeing this
blown99 replied to Tony302600's topic in 6.0L Power Stroke® Diesel Engines
Can someone give me a quick run down on the procedure for checking for air bubbles in the fuel filter housing? I have yet to see any combustion gasses entering the fuel system in the international chassis yet. Now that I just wrote that, there will be one in the lot on Monday morning. Thanks Mark -
The picture you show of the contaminated inj. looks like many that I have removed that had rusty fuel tanks. I still am not sure how it makes it past the filters but it does. Where is he taking his fuel pressure reading from? That is a returnless fuel system. The only port to take a reading from is on the intake/fuel manifold at the top front of the engine on the left side. He will have either a shraeder valve or a compucheck fitting. It is possible to read fuel pressure and not actually have fuel at the inj.. The air gets bound between the inj. and incoming fuel with no where to go because it is a returnless system. To bleed the system he needs to fill the filter housing, depress the shraeder valve/compucheck fitting and use the hand primer to bleed the fuel rail until steady fuel comes out. Does the turbo actuator cycle when the key is turned on? Do the injectors buzz when the key is turned on? Remove the EGR valve and visually make sure it is not stuck open? This can cause a hard start no start. Remove the valve cover. Disconnect the cam sensor so the engine will not start. Energize the IPR valve with power and grounds. Crank the engine and look under the high pressure oil manifold. The injector tops and or pucks may be leaking. (not so much injectors in this case since they were replaced). When he is cranking the engine, it should crank at a normal speed for about 5 seconds and then get bogged down. This is the hpop being worked to the max. Does it do this?
-
Bad rocker arm Tips on 04 VT-365's
blown99 replied to Scott B's topic in 6.0L Power Stroke® Diesel Engines
I've done many of the valve train uptime kits, but only on UPS chassis. I havn't had any problems with headgasket failures afer replacing the center row of head bolts. Always funny how procedures that were not acceptable years ago are now ok when the dime is on them, stop leak to repair front cover leaks, 365 valve tain/head bolts, turbo recons, install plugs vs new block heaters, no more changing injectors for smoke and misfire conditions when cold. -
How about an injector o-ring going bad. If the middle o-ring goes bad, high pressure oil will be forced into the fuel system and either burned as fuel or returned to the filter housing. Ususally the engine does not smoke or have a performance complaint.
-
I install the updated STC joint kit and pry the branch tube back into place. Havn't had any comebacks as a result of prying the tube back into place.
-
6.0 Reflash in a UPS chassis
blown99 replied to blown99's topic in 6.0L Power Stroke® Diesel Engines
Got it all figured out Friday. With the new NETS system they are downloading the info into the truck ECM with the 1939 data line. On ALL the UPS chassis there is to much noise to allow for an uninterupted signal between tthe ecm and the laptop. Internationals tech service told me to put it on another vehicle (did not tell me they changed the way the program was being downloaded) So I used another UPS chassis and ran into the same thing. Programming a normal truck and there is no problem, so I pull up a wiring diagram of the data link on a UPS chassis and one for a Normal truck and compare the two. The major difference between the two is the UPS chassis uses an adaptor module on the 1939 link to convert the ECM signals to run the dash gauges. I removed this module (located inside the cab right behind the steering column) and unplugged the dash and the program went right in. Tried this with the other donor UPS chassis also and it took the program, so I don't think it was a fluke. The normal trucks use the ESC to send/convert ecm signal to run the dash cluster which the ups doesn't have. I should probably call tech back and let them in on this, but then again Matt in programming was an arrogant bastard that wouldn't disclose of any infomation on Internationals changing of the NETS program. I hope this helps you other techs from pulling your hair out, well at least for this type of job. Mark -
Need help reflashing a 6.0 in a UPS chassis. The ecm won't take the program. I've disconected both abs and trans ecu, used the new reprogramming box tied into fuse F-20, set the batt voltage to 13.0 and still nothing. Had UPS bring in another truck that I had previosly flashed and swapped the ECU/IDM and I still got the same thing. Talked to Matt in vehicle programming and finally go something usefull out of him. He said that international changed the way NETS programs, now using the 1939 data link and that every ups car is going to have this problem. He said some techs are jumping power to certain pins and this will allow for the programing process to work. I need to know what pins to put power to. Thanks Mark
-
Everytime I do the valve train updates I worry about having a head gasket failure while on a road test. Every head that I have removed has always been warped, so removing the head bolts one at a time to replace the rocker arms has me wondering if I am disturbing the gasket enough to leak.
-
On the UPS chassis you can remove the valve cover on the left side if you slightly bend the flange under the floor out of the way a 1/4". This will allow you to remove the high pressure oil manifold and an injector but not a head bolt. Its not the most professional procedure but you can save a ton of time on it. I ended up removing the head on the UPS VT365 not because it was bad but because another tech was doing an EGR cooler, and a rear gear train update and found that the engine would not bar over to allow him to remove the torque convertor bolts after he did the EGR cooler. I ended up with the job and found a piece of metal that didn't appear to be from the engine or its accessories sitting on top of #8 piston. For the first one in a UPS van it wasn't that bad, took about 10hrs.
-
The water filter kit comes with pieces of 2 ft hoses that are expected to reach 5 ft, no hardware for the brackets, (a pain because the parts dept. doesn't have metric frame bolts to fit the crossmemeber). I did two of the valve train updates in the past two weeks in the UPS chassis and one left side cylinder head gasket. The head wasn't bad to do once the floor was out. You can remove the valve cover without removing the floor, you just can't get the head bolts out with the floor in.